在胶鞋生产中,胶鞋硫化罐起着核心作用,其工作原理与硫化过程优化直接关系到胶鞋质量和生产效率。
一、工作原理
胶鞋硫化罐的工作基于橡胶硫化这一关键化学反应。天然或合成橡胶在未硫化时,分子链呈线性或轻度支链状,物理性能欠佳,像强度低、弹性不稳定,还容易变形。硫化就是在特定温度、压力和时间条件下,借助硫化剂(常见如硫磺),使橡胶分子链间发生交联反应,形成三维网状结构。
胶鞋硫化罐以蒸汽或其他加热介质为热源,将热量传递给罐内的胶鞋和橡胶材料。蒸汽在罐内积聚产生压力,一方面促使橡胶分子与硫化剂充分接触并反应,另一方面能帮助胶鞋在硫化过程中保持形状,防止变形走样。在此过程中,温度和压力的精准控制尤为关键,合适的温度和压力能加快硫化反应速度,保证交联结构均匀形成,进而提升胶鞋的耐磨性、耐老化性、弹性和强度等物理机械性能。
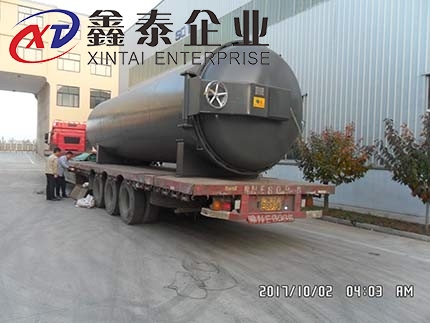
二、硫化过程优化
优化硫化工艺参数
1. 精准温度控制:借助高精度温度传感器和先进的温度控制系统,可实现对硫化温度的精准调节。针对不同胶鞋材质和配方,制定个性化温度曲线。比如在升温阶段,采用分段升温,先低速升温让胶鞋内外温度均匀上升,防止表面过热;保温阶段,将温度波动控制在极小范围,确保硫化反应稳定进行。
2. 合理压力设定:依据胶鞋的结构和尺寸,以及硫化工艺要求,精确设定硫化压力。对于结构复杂或厚度不均的胶鞋,可能需要在不同阶段调整压力,保证各个部位都能充分硫化。同时,利用压力监测设备实时监控压力变化,及时做出调整。
改进硫化罐结构设计
1. 优化加热与循环系统:改进蒸汽进口和分布方式,让蒸汽在罐内均匀分布,避免局部温度过高或过低。比如在罐内安装导流板或扰流装置,增强蒸汽循环流动,提高热传递效率。此外,采用高效保温材料,减少热量散失,降低能源消耗。
2. 提升装料与卸料系统:设计合理的装料方式,如采用分层、分格的硫化车,进一步优化胶鞋在罐内的摆放,确保每双胶鞋都能均匀受热和受压。同时,升级卸料系统,实现快速、安全卸料,减少硫化后胶鞋在高温环境下的停留时间,降低因冷却不及时导致的质量问题。
引入自动化与智能化控制
1. 自动化操作流程:利用可编程逻辑控制器(PLC)实现硫化过程的自动化控制,涵盖蒸汽通入、温度调节、压力控制、硫化时间计时以及降温、卸料等环节的自动执行。这不仅减少人工操作误差,提高生产效率,还能保证每批次胶鞋硫化过程的一致性。
2. 智能监控与数据分析:通过安装智能监控系统,实时采集硫化过程中的温度、压力、时间等数据,并进行分析处理。根据数据分析结果,及时发现潜在问题,如设备故障隐患、工艺参数偏差等,并自动调整或发出预警,为生产过程的优化提供数据支持 。
通过深入了解胶鞋硫化罐的工作原理,并积极对硫化过程进行优化,胶鞋生产企业能够有效提升产品质量,提高生产效率,在市场竞争中占据更有利的地位。
如果还想在短文中增加实际案例、成本分析等内容,欢迎随时告诉我,我会进一步完善。